PRODUCTION/QUALITY
Quality is the heart of
our production process
Customer service is one of the distinctive characteristics of MF Catenificio Frigerio. Quality is the result of a series of precise choices which start with the selection of raw materials and continue with the development of structured industrial processes, through which the products are tested and improved in order to satisfy the end customer.
Planning
Close to the customer right from the planning stage
The technical department is able to offer a wide range of consultancy to identify the most suitable solution – in terms of design, raw material to be used and treatment to be carried out – to meet the particular requirements of chain use.
The experience and specialisation acquired in over sixty years of activity allows the technical and commercial staff of MF Catenificio Frigerio to work side by side with the customer, putting their wealth of knowledge and expertise at their service.
The modern in-house mechanical workshop ensures that the production systems are ready to be equipped for any type of production required.
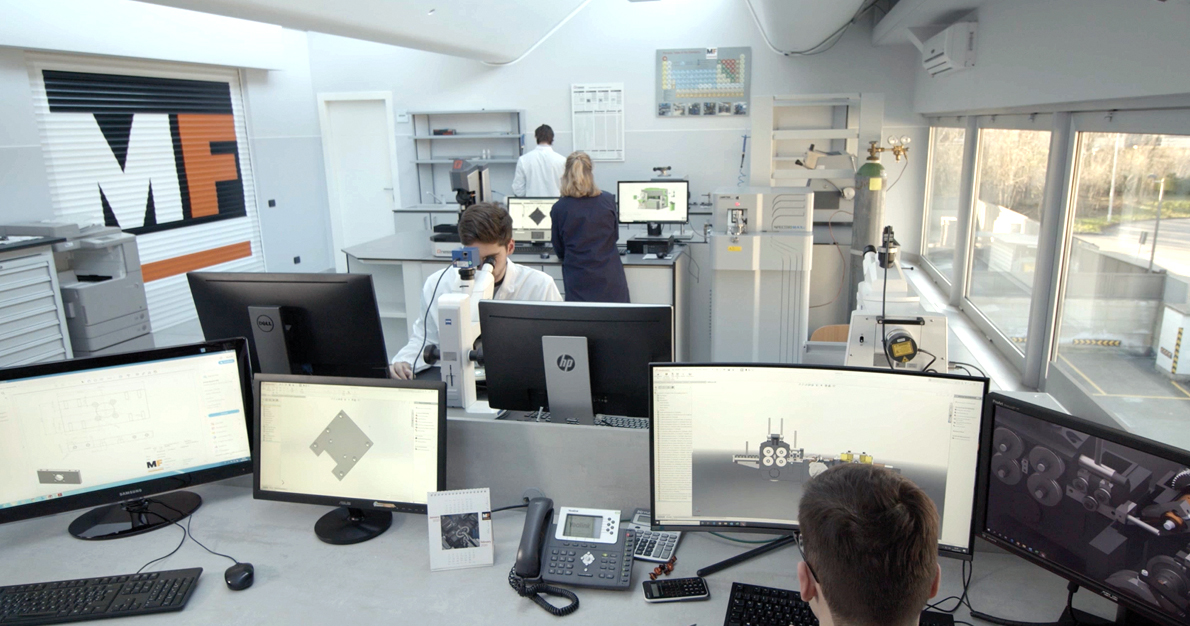
Production cycle
A process under control. At every stage.
The quality of the final product is guaranteed by a production process that is controlled at every stage, starting with the procurement of the specific raw material to be used from leading national and foreign steel mills that certify its characteristics. Production is carried out on 16 different work islands, each of which employs machines specialised in processing chains that differ in thickness and type of link. Each island has a fully automated processing cycle, according to the programming set by the operator: the wire is first drawn, then bent, chained and finally welded.
The presence on each plant of in-line drawing machines for calibrating the chain makes it possible to carry out a 100% check on production and to ensure the exact dimensional conformity of each individual link. A further dimensional check is carried out at the final stage using a special pass/fail gauge. The MF Catenificio Frigerio plants have a total daily production capacity of 50 tons of chain, with links of different designs and diameters ranging from 3 to 22 mm.
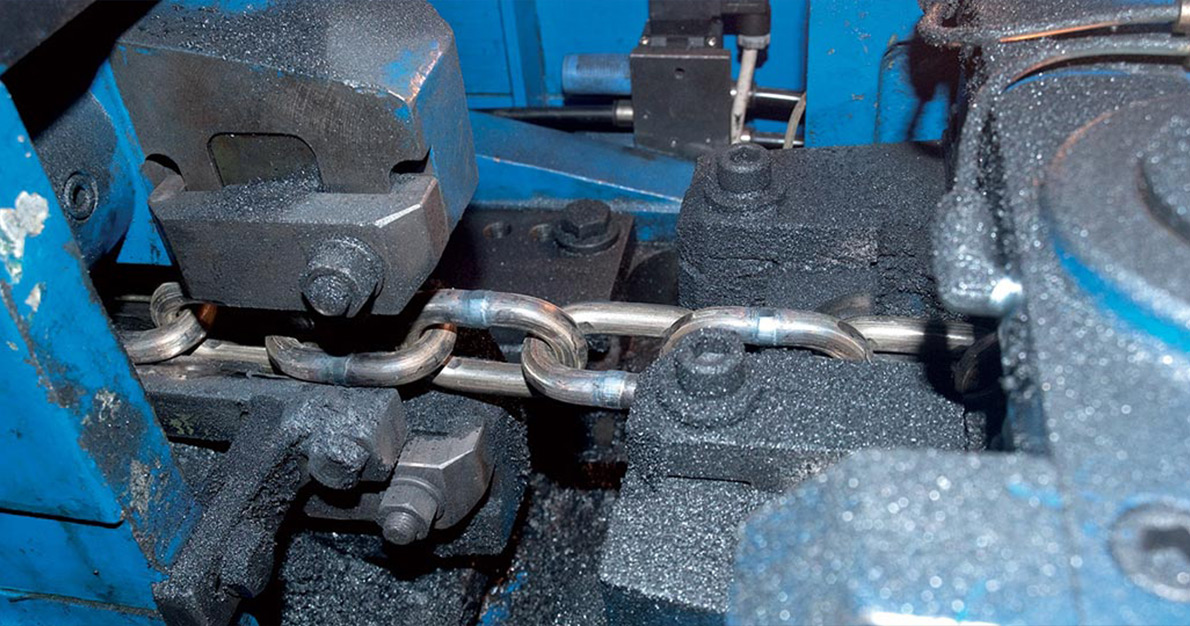
Treatments
Treatments tailored to each specific use
To give the properties required by each customer, each batch of chain undergoes specific finishing treatments, depending on the structural and aesthetic characteristics to be obtained. Electrolytic galvanisation gives the chain a particular brilliance, although with a low coating and reduced resistance to salt spray. Hot-dip galvanising, on the other hand, increases corrosion resistance by immersing the chain in molten zinc, thanks to the increased thickness of the protective layer. To increase the wear resistance of the steel, the chain undergoes a heat treatment of carbocementation, which enriches the surface with carbon. The hardening and tempering process is carried out on those steel chains that require high tensile strength. Finally, the epoxy painting process is used for some products.
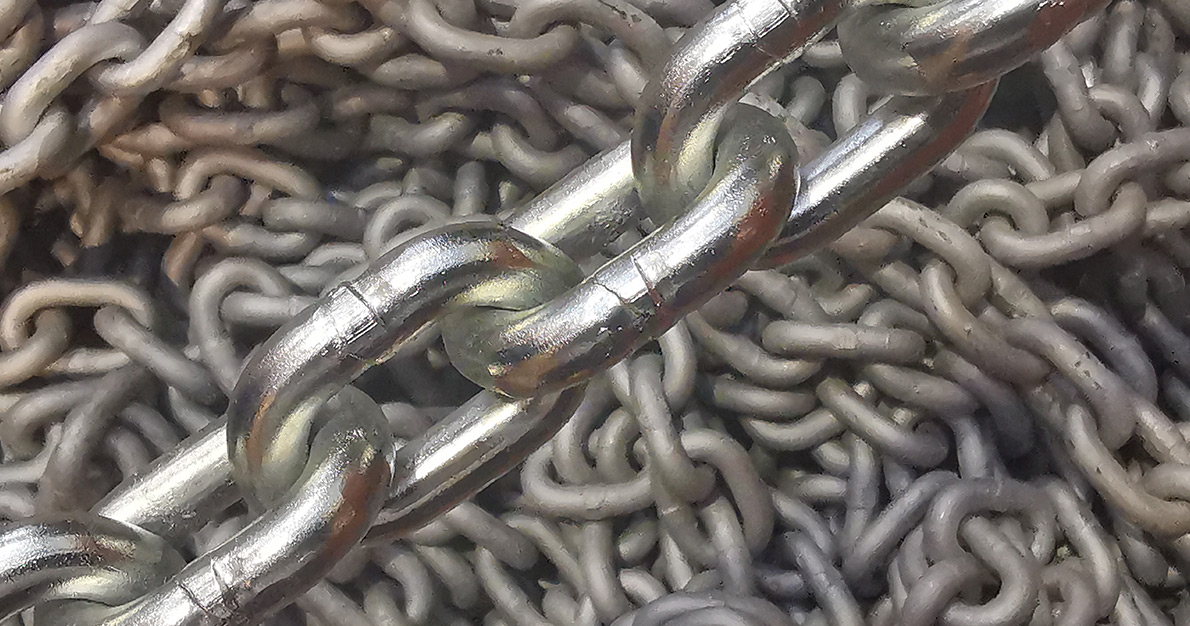
Quality
The utmost attention to every single detail
Guaranteeing the customer the quality of the end product has always been one of the prerogatives of MF Catenificio Frigerio.
For this reason each batch of chain produced is subjected to a series of strict load traction, breaking and bending resistance tests which test the physical and mechanical characteristics under conditions of maximum stress, with particular regard to the perfect seal of the weld. All parameters are recorded and stored in the company computer archive. The maximum attention to every single detail is also translated into accurate optical inspections to highlight any imperfections.
MF Catenificio Frigerio has a UNI EN ISO 9001 certified quality system which covers the entire company process.
This system, built on the basis of a series of well-defined procedures, which regulate every single phase – from design to production and logistics and warehouse management. is a further guarantee of reliability for the customer.
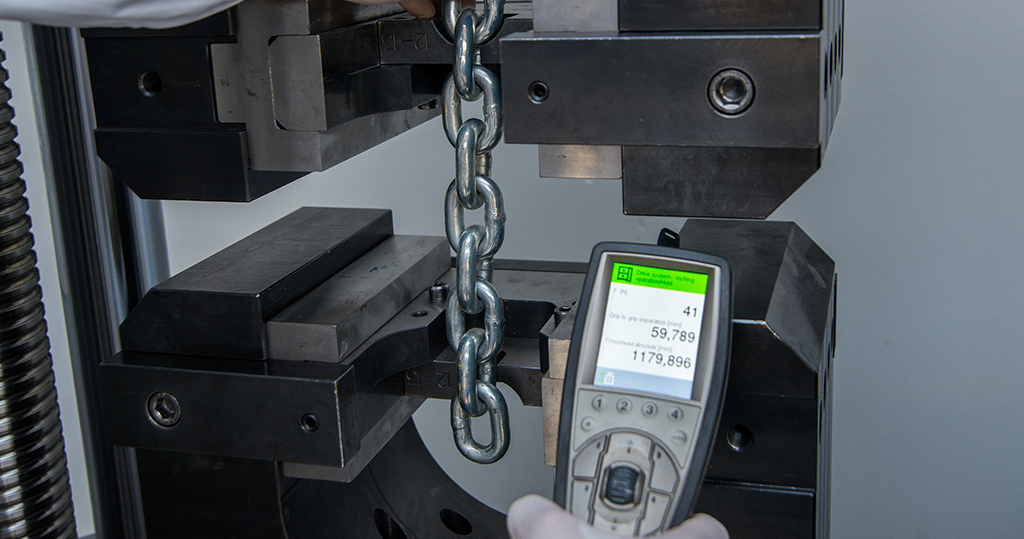
The quality laboratory
A point of reference in many processing stages
The Quality Laboratory is a reflection of MF’s constant quest for improvement.
Our technicians carry out a wide range of tests in close contact with R&D and Quality Control to improve the performance of the chains in relation to their specific application.
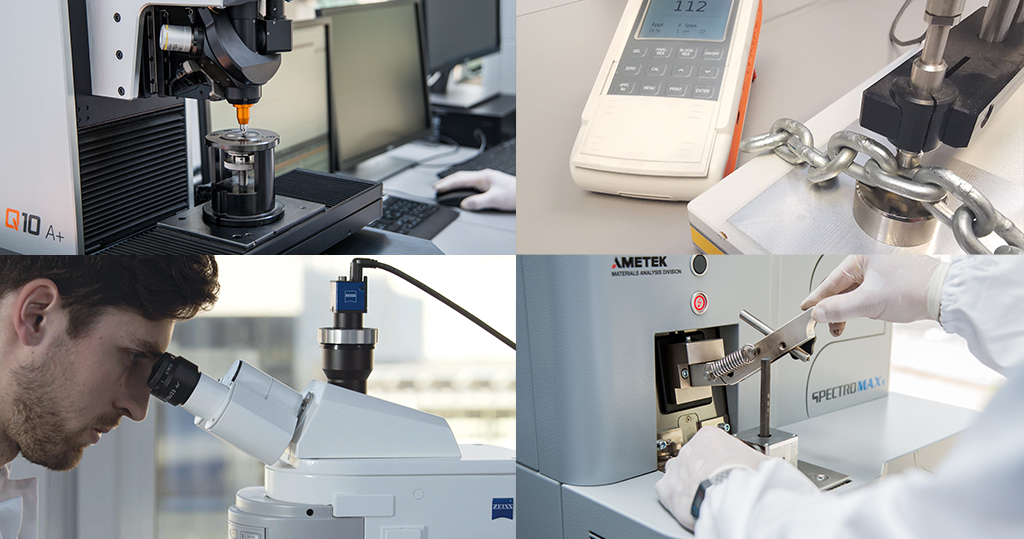
The MF gauge
An indispensable tool to check chain calibration
MF, with its long experience in chain manufacture, has made the inspection tools (gauges and plugs) in-house to validate the tight tolerances of conveyor chains.
the control instruments (gauges and plugs) to validate the tight tolerances of conveyor chains. MF’s gauges are unique in their ability to handle all the checks required to ensure a quality product. The gauges allow simple non-passing operations to eliminate measurement errors or misinterpretation of measurements.
MAXIMUM TOLERANCES FOR CONVEYOR CHAINS
Given L as the length of the brim, the maximum overall tolerance of the chain, unless otherwise specified, is 0.45% of L. The deviation between two coupled chain brim is, unless otherwise specified, a maximum of 3 mm (for brim lengths up to 12 metres).
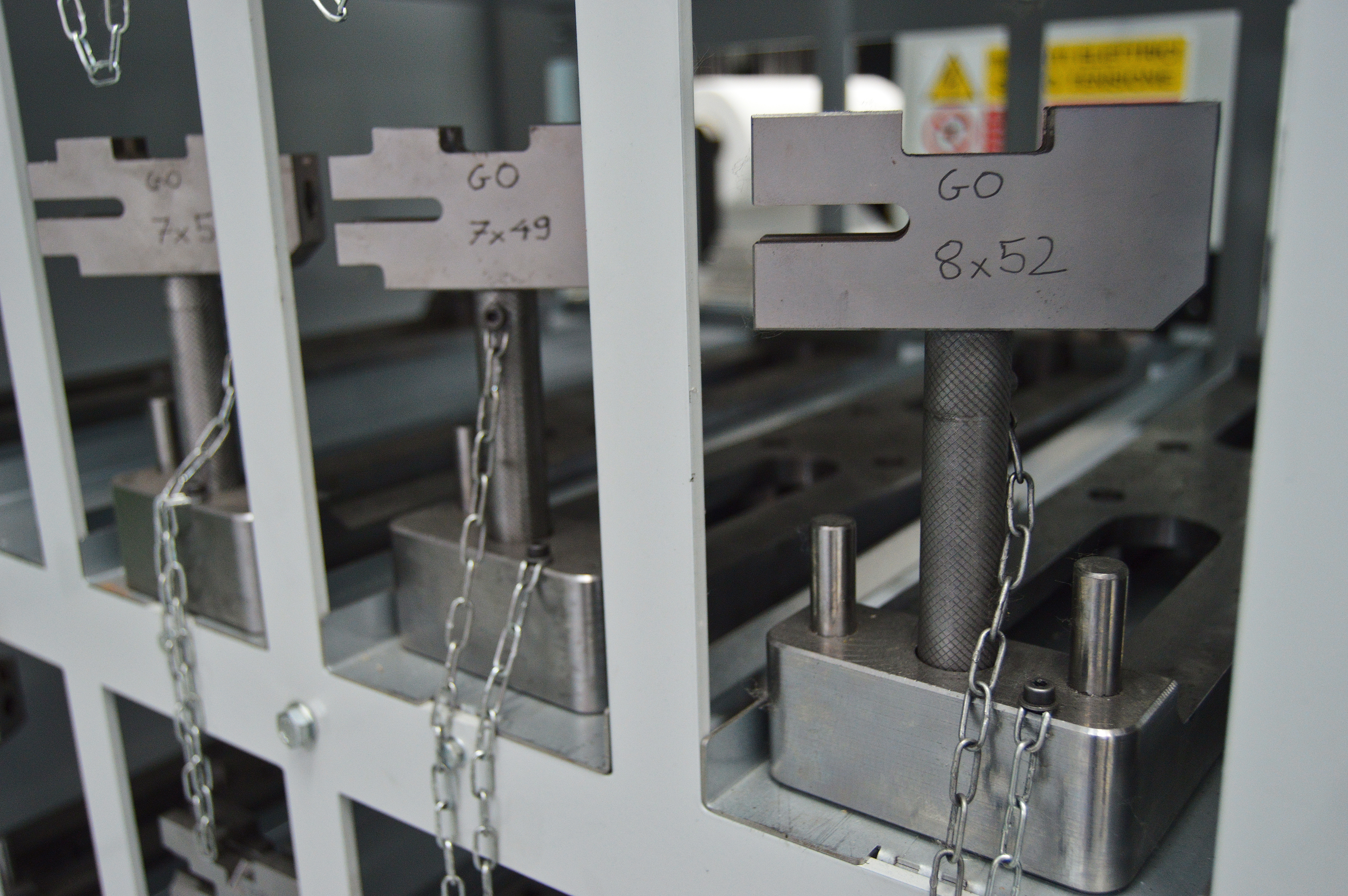